
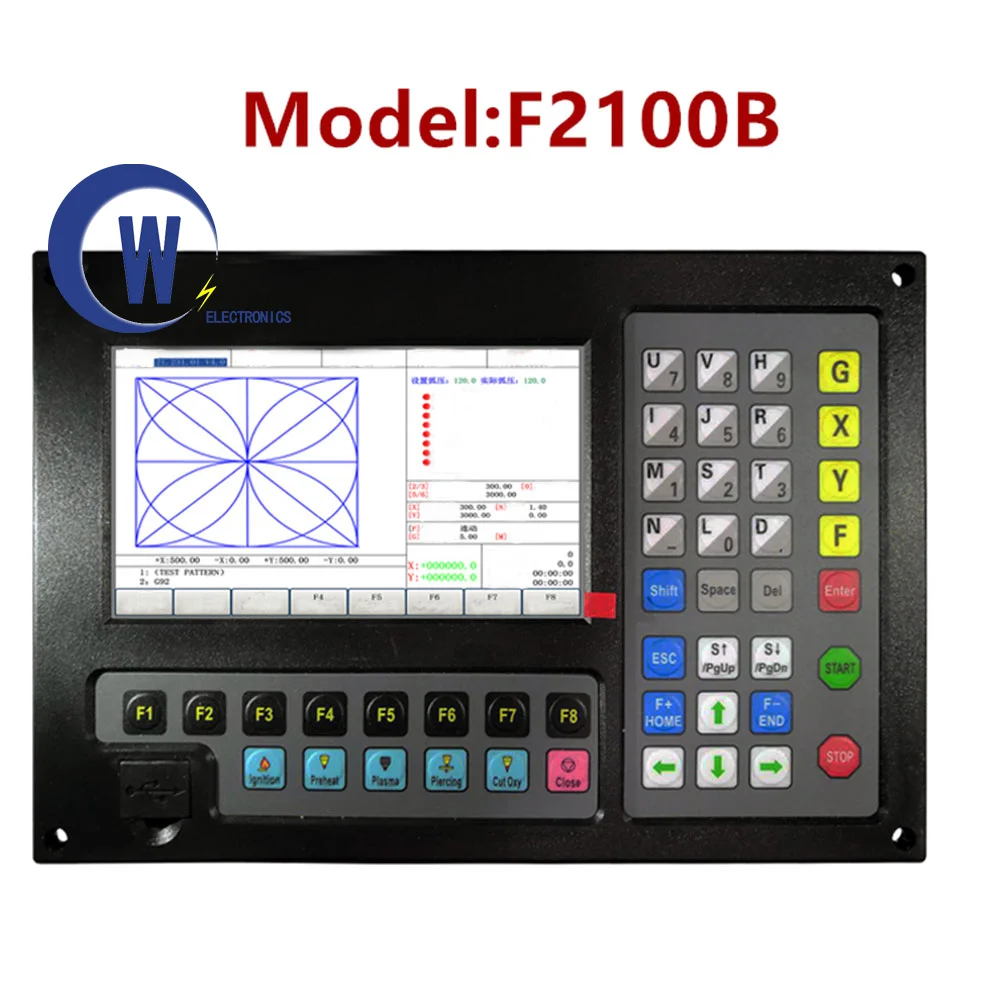
Their antifoaming potential has likely been underestimated because the typical contact area between foam and surface is small. Here, we demonstrate that liquid-repellent coatings show excellent antifoaming properties. Surprisingly, the consequences of liquid-repellent coatings on defoaming and antifoaming have not been explored. These standing issues make alternative approaches highly desirable. Therefore, they might need to be removed afterward, requiring subsequent energy-intensive separation processes 1, 5, 6. Although efficient, oils and/or particles can be environmentally harmful while also altering the properties of the final product. Alternatively, oils can also be used independently for defoaming 2, 3, 6. To circumvent this, oils are used as carrier fluids to deliver hydrophobic particles directly to the thin film separating neighboring bubbles 5, 6. However, hydrophobic particles quickly become inactivated by surface-active surfactants, which are always present in foams. The effects of size, shape, and degrees of hydrophobicity of microparticles on defoaming have also been intensively studied to optimize defoaming 2, 3. The agents enhance the coalescence of foam bubbles by speeding up the disintegration of bubble films 3, 9. These chemicals are also known as defoaming or antifoaming agents and include oils 4, hydrocarbons or waxes 4, 5, microparticles 2, 3, 6, 7, or mixtures 1, 8 of these. This is achieved respectively, by depositing chemicals onto bulk foams or within the target liquid. This mode of interfacial destabilization offers untapped potential for developing efficient, low-power and sustainable foam and froth management.ĭefoaming is the process of destabilizing existing foam while antifoaming aims to prevent the formation of foam 1, 2, 3, 4. Microscopic imaging reveals that amphiphobic nano-protrusions directly destabilize contacting foam bubbles, which can favorably vent through air gaps warranted by a Cassie wetting state. They significantly improve retraction of highly stable wet foams and prevention of growing dry foams, as quantified for beer and aqueous soap solution as model systems. Here, we show that passive defoaming or active anti-foaming is possible simply by the interaction of foam with chemically or morphologically modified surfaces, of which the superamphiphobic variant exhibits superior performance. However, such additives may need to be later separated and removed for environmental reasons and product quality. To speed up defoaming or enable anti-foaming, liquid oil or hydrophobic particles are usually added. Uncontrolled foaming results in product losses, equipment downtime or damage and cleanup costs.
FASTCAM OUTLINE CRACKED
FASTCAM OUTLINE PRO
FASTCAM OUTLINE FULL
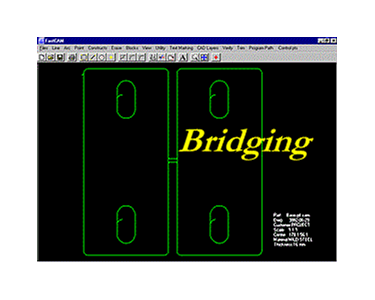
Fully integrated Drawing Editor (as above).A full featured, fully automated NC solution.This is a full featured, fully automated system with a focus on saving time, plate and piercing. Where machines are fully utilised every day of the week with a variety of jobs, the customer will reap the benefits using the very latest in advanced cutting technology.
FASTCAM OUTLINE PROFESSIONAL
FastCAM Professional – High Duty Cycle For businesses that may get five different jobs with multiple parts and thicknesses.
